SIS(Sampling Intelligent Scan)
- Do you have problems getting AFM topography data from your samples?
- SIS completely changes the concept of what is possible when it comes to AFM topography measurements.
- SIS provides stable and precise control of the AFM probe to quickly and accurately measure the topography and material property of your sample.
1-1. Issues with Conventional DFM (Tapping) and Solutions by SIS
1-1 Issues with conventional scanning methods
(1) Deteriorated Tracking Performance on Down Slope Area (Parachuting )
Diagram 1-1: Correct topography information is unobtainable if the probe tracking on the sample is poor.
While increasing the feedback gain can lead to a better tracking performance, it may cause damage to the AFM tip and introduce oscillation noise due to the high gain setting.

(2) Contact-Mode-Induced Damage on Soft or Sticky Samples
Under contact-mode AFM, the surface of most soft samples is easily damaged by the lateral force that intrinsically exists when the tip is moving across the surface. In addition, stable imaging is more difficult to achieve if there is a large adhesion force between the tip and the sample (even though the probe force is minimized to improve the AFM imaging).
In the case of current measurements via conductive AFM, we usually need a high probe force in order to decrease the contact resistance between the sample and the probe. As a consequence, it could cause even more damage on the sample surface.

(3) Material Property Artifacts When Imaging by Phase Mode Using Conventional DFM (Tapping)
In material property measurements, you may encounter an artifact at both edges of a surface feature due to the impact of topography on AFM measurements.

1-2 About SIS
SIS (Sampling Intelligent Scan mode) is able to control the scanning speed based on the sample topography and only keep the probe engaged with the sample surface at each measurement point (i.e., each pixel) as it collects the morphology and material property information. After that, the probe is automatically withdrawn before it moves laterally from its current location to the next measurement point.
Fig.1-4 shows the probe motion during data acquisition by DFM and SIS. Data-acquisition points are shown at the red arrows. In DFM, the probe is continually engaging the sample surface, even as it scans along the sample. In SIS, the probe only engages the sample surface when it collects sample information. Therefore, SIS involves significantly reduced tip/sample interactions, and thus helps minimize tip wear and maintain probe sharpness, which is crucial for AFM high-resolution imaging. SIS can also eliminate the lateral/friction force since the probe only moves in the Z direction when it approaches, engages, and disengages the sample at each measurement point. This protects the surface of the sample from damage imposed by the tip dragging during the scan.

Fig. 1-5 shows the probe motion by SIS during the scanning on the sample surface. The probe only engages the sample surface at each data-acquisition point, and then withdraws from the sample surface to move to the next acquisition point. SIS automatically increases the acquisition speed over flat or downhill regions of the sample, decreases the scanning speed, and further withdraws the probe to avoid crashing as it travels uphill. The smart probe motions guided by SIS are shown in Fig.1-4 and Fig.1-5.

Feature1 : Reducing the probe wear
Tip/sample interactions only at data acquisition points.
Feature2 : Eliminating lateral/friction forces during AFM measurements
No lateral/lateral force at each measurement point. More stable and better controlled tip/sample interactions.
Advantages of topography measurement with SIS
- Topography measurement for rough sample (SIS allows the use of a high aspect probe, more stable than DFM).
- Good for soft or adhesive samples.
Advantages of material property measurement with SIS
- Phase imaging for material property measurement with no artifacts.
- Stable electrical-property measurement for soft conductor and organic semiconductor materials with no sample damage.
- Material property measurement allowed with diamond coated probe.
Fig. 1-5 Probe motion by SIS.
The AFM probe is continually in contact with the sample during conventional contact mode imaging. In conventional DFM (i.e., tapping mode), the probe is oscillating at its resonant frequency and has intermittent contact with the sample during the scan. The measurement modes operated with SIS are noted as SIS-AFM and SIS-DFM. For brevity, the application of DFM and AFM operation controlled by SIS is simply abbreviated as SIS when either DFM or AFM mode has been already clarified in a specific application case.

2. SIS Application Examples for Topography and Material Property Measurements
(1) Polytetrafluoroethylene sheet by DFM and SIS
Fig. 2-1 shows topography images of a polytetrafluoroethylene sheet (PTFE, a.k.a. Teflon) acquired by DFM and SIS, respectively. The image obtained by DFM shows that the sample is micrometer-scale rough, and often causes a tip sliding/drift issue along the direction of scanning (known as parachuting) due to poor tip tracking of the surface morphology. However, in the SIS-obtained data, the surface topography is much sharper in higher resolution.

(2) Phase imaging of a grease sample by DFM and SIS
Fig. 2-2 shows the observation of high-mobility grease by DFM and SIS. Due to the adhesive/sticky nature of this sample, wavy noise is observed in both the topography and phase images obgained via the conventional DFM mode. In contrast, clear topography and phase images without any wavy noise were obtained via SIS at the same sample location.

(3) Soft and highly adhesive samples by DFM and SIS
Shown in Fig. 2-3 is an application example of an adhesive material imaged by DFM and SIS-DFM. In DFM, there are many noise lines shown along the scan direction of the image. However, SIS is able to image clearly without lateral line noises. Fig. 2-4 shows a chromosome in liquid measured by DFM and SIS-DFM. Similarly, line noises and spike noises at locations marked by red arrows were observed in the DFM image, while clear images without such noises were acquired via SIS.


(4) Solid polymer electrolyte membrane by conventional-phase and SIS-phase imaging
Fig. 2-5 shows an application example of both DFM and SIS-DFM imaging of a solid polymer electrolyte membrane for fuel cell applications. Though DFM under a feedback is supposed to maintain the amplitude of probe oscillation at a preset level and despite this being a homogenous sample, contrast variations corresponding to the surface topography are captured in both the amplitude and phase images. By contrast, error signals are greatly reduced in the SIS-phase and SIS-amplitude images.

(5) Lamella crystal/PET sheet by DFM and SIS-phase mode
Fig. 2-6 shows an application example of AFM imaging of dispersed lamellar crystal within a PET sheet by using DFM and SIS. In the DFM-phase image, the left edges of lamellar crystals exhibit a brighter contrast and the right edges were correspondingly dark due to the error signals included by the impact of the tip with the surface topography. In SIS-phase mode, contrast variations are consistent with the compositional mapping. Fig. 2-7 shows the relationship between topography, material composition, and phase by DFM and SIS in the pattern diagram.


(6) Advantages of material property measurements via SIS
Fig. 2-2 shows that SIS allows for better topography and phase imaging of a grease sample than DFM due to the elimination of the lateral/friction force. Fig. 2-3 and 2-4 also show SIS-enhanced imaging of chromosomes in liquid and adhesive materials. The differentiations in terms of the lateral forces among the AFM/DFM/SIS are illustrated in Fig.2-8. The elimination of the lateral force can reduce undesired cross talk between surface topography and simultaneous analysis of other properties. As a result, AFM data with improved accuracy and better resolution can be expected using SIS.

(7) Adhesive material by DFM-Phase and SIS-Phase
Fig. 2-9 shows material property imaging by DFM-Phase and SIS-Phase on the same adhesive material used in Fig. 2-3. As shown, resolution is greatly increased in both the topography and phase images acquired by SIS.

3. SIS Application Examples for Electrical Property Measurement
(1) Soft conductive material by AFM-Current and SIS-Current
Sometimes, in order to prevent the probe from damaging the sample during a contact mode scan, the force between the probe and the sample needs to be reduced. However, there are some particular imaging modes, such as conductive AFM (C-AFM) and SSRM, which actually require a fairly high force between the probe and the sample to reduce the contact resistance and ensure good current measurements. In such situations, the probe may cause damage to the sample during the scan. Fig. 3-1 (a to c) shows some example data of this situation by AFM-Current. In Fig. 3-1 (a), the yellow arrow shows a pattern diagram of the direction and magnitude of the detected current. In addition, the dragging of the tip across soft samples can lead to a poor resolution due to the laterally imposed force. As a result, spikes (or line noise) are observed in both the topography and current images (Fig. 3-1 (b, c)). In contrast, the SIS scan shows a very stable measurement for both topography and current (Fig. 3-1 (e, f)).

(2) Si dopant step calibration sample by AFM-SSRM and SIS-SSRM
SSRM (Scanning Spreading Resistance Microscope) uses a conductive diamond-coated probe with a high spring constant to map the dopant density of semiconductor samples. An undesirable side effect of this type of scan is that these special diamond probes scratch the oxide layer of the Si device in order to reduce the contact resistance, which may have the consequence of affecting the electrical property during mapping. Fig. 3-2 shows a Si dopant step sample imaged by conventional AFM-SSRM and SIS-SSRM. With the AFM-SSRM technique, it shows some fluctuation (line noise along the scan direction) in the resistivity image. Using SIS-SSRM, the resistivity image is clearer and more stable than AFM-SSRM and better resolve the dopant density differences on the sample.

(3) Leak-current mapping of aluminum-oxide thin films (AFM-Current vs. SIS-Current)
As previously mentioned, the SIS mode can prevent sample damage and instability of electrical property signal during conventional contact-mode-based AFM techniques. Here is an application example where the sample was not damaged with conventional AFM-Current. Fig. 3-3 shows a current distribution mapping of aluminum-oxide thin film by AFM-Current and SIS-Current. Both modes are measuring the current with a negative bias voltage on the sample. In this case, the dark region have a leaking current in the current image. Fig. 3-3 (a) and (b) show the topography and current image by AFM-Current, and Fig. 3-3 (c) shows an overlaid image of both. There are two big leak-current spots on the grain boundaries. Fig. 3-3 (d) and (e) show the topography and current image using SIS-Current, and Fig. 3-3 (f) shows an overlaid image of both. You can see there are two big leak-current spots on grain boundaries, the same as the AFM-Current. However, on the AFM-Current image there are some artifacts of lateral line noise toward the scan direction, and the leak-current spot size is larger than it is in the SIS-Current image. Due to this, we can deduce that the SIS-Current is more stable than AFM-Current and should be a preferred method for current mapping due to the reduced lateral line noise.

(4) Piezoelectric response mapping of ferroelectric thin film (AFM-PRM vs. SIS-PRM)
PRM (Piezoelectric Response Microscopy) (Fig. 3-4 (a)) can detect the piezoelectric response in a sample in both the vertical and horizontal directions (Fig. 3-4 (d)). Fig. 3-4 shows the results of the piezoelectric response in the horizontal direction of a ferroelectric thin film by both conventional AFM-PRM and SIS-PRM scans. Bright contrast means the polarization to the left, and dark contrast means the polarization to the left in the PRM image. The SIS-PRM scan shows a definite improvement in imaging the grain boundaries and the domains inside the grains.

4. Application Examples with SIS
(1) Highly crystallized PVDF (polyvinylidene fluoride) with SIS-PRM
PVDF (polyvinylidene fluoride) is a ferroelectric polymer which shows promising potential for sensor and electronic device applications. Fig. 4-1 shows the piezoelectric response mapping of highly crystallized PVDF by SIS-PRM. Fig. 4-1 (a) shows an optical image of highly crystallized PVDF that was imaged using polarized microscopy, since these spherulites cannot be resolved with a regular epi-illuminated objective. In Fig. 4-1 (b) and (c), the SIS topography and SIS-PRM images show a domain with reversed polarization in the vertical direction in the center of the spherocrystal. Bright contrast area on the SIS-PRM image means the direction of arrow to the screen; dark contrast is opposite direction of arrow to the screen.
Sample courtesy of Mr. Kunitoshi Koji, Analysis Engineering Department, Nitto Denko Co., Ltd.

(2) Conductive polymer (PEDOT-PSS) coated surface by SIS-Current in vacuum
Fig. 4-2 shows current mapping in vacuum by SIS-Current under a bias of 3 V of the conductive polymer PEDOT-PSS [Poly (3,4-ethylenedioxythiophene)-poly (styrenesulfonic acid)] coated on a glass substrate. High-resolution mapping of conductive domains is seen as tiny bright dots and are clearly resolved in the current image.
Sample and Data courtesy of Mr. Kunitoshi Koji, Analysis Engineering Department, Nitto Denko Co., Ltd.

(3) Ternary Lithium-ion Battery Positive Electrode Active Material Li (Ni-Co-Mn) O2 Imaged by SIS-SSRM in Vacuum
The ternary lithium-ion battery positive electrode active material Li (Ni-Co-Mn) O2 is often used in vehicle batteries. Fig. 4-3 shows images of the material produced by SIS-SSRM after being processed by ion-milling cross section. As for the topography image in Fig. 4-3 (a), the surface that was processed by flat ion milling. As for the SIS-SSRM image in Fig. 4-3 (b), resistivity distribution which reflects the material and internal structures (conductive path) is shown. Most of the active material which has a round shape has a resistance value of approximately 100 MΩ, which is shown in Yellow to Green on the color scale. There is also a conductive auxiliary agent which has carbon (C) as the main ingredient in the gap between the active materials. They have a resistance value less than 1 MΩ, and is shown in the Blue to Purple area on the color scale. The following link provides more detailed information about the images produced by SIS-SSRM. The linked page explains more about these regions, such as the red-colored donut shape of high resistivity, the round bright-blue shape on the right of the image which has a resistivity of approximately 10 MΩ, and the rectangular orange area which has resistivity of 1 GΩ.
⇒ AFM application data sheet No.013 [Observation of the ternary lithium ion battery positive electrode active material Li (Ni-Co-Mn) O2 by SEM (EDX)-SSRM with air protection holder.]
Fig. 4-2 (c) shows a differential-AFM image and in this case, shows the surface morphologies better than the topography image. You can see slight artifacts from the ion-milling process. Fig. 4-3 (d) is an overlaid image of the differential-AFM and SSRM images. From these images, you can see that the electric resistance distribution that was measured by SSRMs has no correlation with the uneven surfaces, which gives us confidence to say that the color-SSRM information is based solely on the composition inside the material and its conductive path.

(4) Observation of Lithium-ion Battery Positive Electrode Material by SIS-Current in Vacuum While Gradually Changing the Bias Voltage.
Fig. 4-4 shows an SIS-current image of a lithium-ion battery’s positive electrode material in vacuum as the bias voltage is gradually changed. While applying a low bias voltage, currents are only detected in the highly conductive carbon areas. As the bias increases, you can see currents start to flow into the regions containing the active material of lithium cobaltite (LCO). Thus, a bias-dependent behavior is observed.
Sample and Data
courtesy of Mr. Kunitoshi Koji, Analysis Engineering Department, Nitto Denko Co., Ltd.

Product lineup
Hitachi AFM will prove useful at any stage
By application
Automation / Ease of use
High accuracy / High resolution
- High-accuracy measurements of slanted surfaces with a steep slope
- High-accuracy measurements without damaging samples
- High-resolution measurements in a vacuum
- Stable and accurate measurements during sample heating and cooling
- High-accuracy topography measurements
- High-sensitivity MFM measurements in ambient or vacuum environments
- Humidity control / observations in liquid
Physical property measurements /
Environmental Controls
- Measurements of work functions in ambient or vacuum environments
- Observations of dopant distribution
- Quantitative measurements of elastic modulus
- Observations of structural changes in a vacuum
- Enabled true observations of topography and other physical properties
- Enabled quantitative measurements during sample heating and cooling
This section introduces applications (actual measurement cases) for scanning probe microscopes (SPM/AFM).
Information for product users
This section offers information aimed at customers who use our scanning probe microscopes.
For first-time users
Related topics
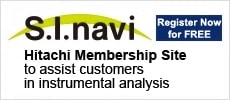
“S.I.navi” is Hitachi Membership Site for analytical instruments users.
“S.I.navi” provides helpful information for daily analysis.